Congestion at busy logistics and transport sites is a problem that can cripple supply chain efficiency. Congestion impacts the entire transport ecosystem, from increased detention costs to operational inefficiencies. However, adopting an advanced end-to-end Transportation Management System (TMS) provides a powerful solution to this problem. Connected end-to-end platform TMS systems have functionality to help streamline site operations, reduce congestion, and improve overall supply chain performance.
The Problem of Site Congestion
Site congestion is not just a logistical issue; it's a financial one. It triggers problems that create a ripple effect throughout the supply chain, ultimately leading to significant profit losses. In essence, every minute of transport downtime translates to financial losses. Here's a few reasons why site congestion is a problem:
1. Increased detention time: One of the most immediate impacts of site congestion is the long wait times for carriers loading and unloading. In peak times, trucks often spend hours idling at sites, waiting for their turn. Research suggests that in the US, trucks spend on average 119 minutes at pick up or drop off sites waiting to be loaded and unloaded. This wastes valuable time, increases detention costs, and delays subsequent deliveries and pickups, creating a bottleneck that disrupts the entire logistics flow.
2. Customer dissatisfaction: The delays caused by site congestion affect the immediate delivery, other stakeholders in the supply chain, and, most critically, the end customers. In today's fast-paced market, these disruptions can tarnish the reputation of logistics providers and, over time, lead to a loss of business.
3. Increased errors: When operations are rushed to compensate for delays due to site congestion, the likelihood of errors increases. Mistakes in loading and unloading can lead to incorrect shipments and consignments, damage to goods, and other costly errors. These mistakes incur additional costs and further delay the supply chain.
4. Operational inefficiency: Congestion results in overall operational inefficiency. Resources are wasted as trucks and drivers spend unnecessary time waiting. This inefficiency drives up operational costs, reducing the profitability for different supply chain stakeholders.
Advantages of a TMS in Managing Site Congestion
Implementing a TMS can help manage site congestion and provide significant relief from the issues it causes. Here are a few advantages of a TMS in managing site congestion:
1. Improved communication: A TMS facilitates seamless communication between site staff, carriers, corporates and other supply chain stakeholders. Real-time updates and alerts keep everyone connected and informed about the status of jobs, reducing misunderstandings and ensuring everyone is on the same page.
2. Better resource allocation: By implementing a TMS, site staffing and equipment can be allocated more effectively. By understanding peak times and operational demands, site managers can ensure the right resources are available, reduce idle times, and improve efficiency, in order to ease site congestion.
3. Automated processes: TMS platforms automate and digitize manual processes, such as planning and scheduling, bookings, communication, pricing and reconciliation. Automation streamlines transport operations and reduces human errors, contributing to smoother workflows, increased productivity, and less congestion.
4. Enhanced coordination: A TMS enhances coordination among various stakeholders in the supply chain. Whether coordinating with suppliers, carriers, or site staff, a TMS ensures everyone is aligned by having access to the same data, reducing delays and improving overall efficiency.
5. Real-time tracking: Real-time tracking provides better visibility into the movement and progress of jobs. Knowing the location and status of each booking helps to manage site operations more effectively, ensuring that trucks arrive and depart as scheduled.
6. Reduction in detention costs: A 2018 study from the U.S. Department of Transportation’s Office of Inspector General found that truck drivers lose approximately $1.1 billion annually in earnings because of detention time. Through digitization, optimization, and improved communication, a TMS helps reduce detention costs. Trucks spend less time waiting at sites, leading to quicker turnarounds, more efficient logistics operations, and a reduction in congestion at sites.
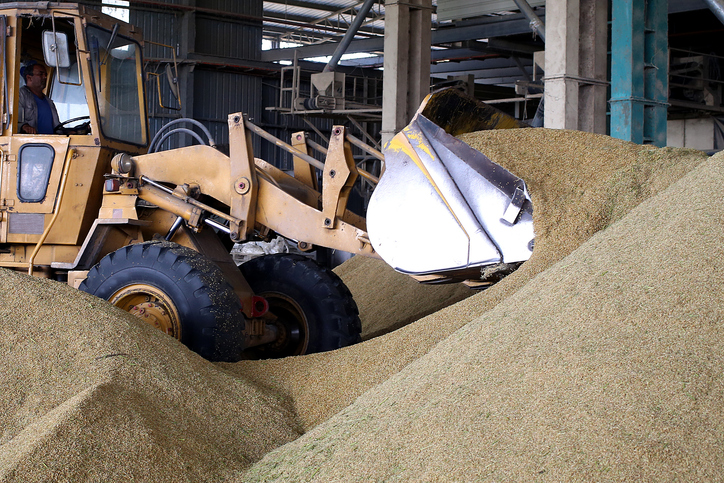
How M2X Site Management Excels
M2X Site Management takes TMS capabilities a step further, offering unique features that specifically address site congestion issues. Here are some of the key features of Site Management in the M2X Platform:
1. Real-time visibility: The M2X dashboard offers clear visibility across all transport movements. Arrival boards provide an overview of inbound and outbound transport, helping site staff manage operations more effectively and anticipate congestion before it occurs. Site staff gain real-time visibility into site activities, enabling faster response times when things change and forward planning for efficient execution.
2. Slot management: M2X’s booking slot functionality allows carriers to book a specific time at which they expect to arrive at the site. This feature allows site staff to schedule precisely and efficiently manage the arrival and departure of carriers to maximize resource utilization and avoid congestion. Booking slots in advance reduces congestion at sites as carriers arrive at their designated time slot instead of all turning up at the same time. This minimises overlaps and delays, ensuring a smoother flow of operations.
3. Improved communication: Being connected in one digital ecosystem ensures seamless communication between site operators and transport providers, reducing delays and improving efficiency. Carriers can send ETAs and delay notifications to sites, keeping them updated with the latest arrival times and any changes to bookings. This allows site staff to schedule effectively and enables proactive planning and communication, improving congestion management.
4. Reduction of manual processes: M2X Site Management streamlines transportation operations and reduces manual processes through data digitization and automation. This digitization removes the daily paperwork, emails, and phone calls that site staff usually have to make, significantly improving productivity and cost savings and minimizing errors.
M2X Customer Success
Ballance is one of our customers using M2X Site Management. As New Zealand's largest fertilizer co-operative, Ballance Agri-Nutrients operates over 130 service centers, consignment stores, and self-service silos nationwide. One of the biggest challenges for Ballance before M2X was peak-time site congestion, which created difficulties for their carriers and service center staff.
The digital workflow of the M2X system allows Ballance site managers to visualize their entire transport network. Using the M2X site functionality, staff can see all bookings coming in and out of their site that day and the details for each, assign site staff to specific jobs, and have their carriers book time slots using the M2X booking slot system.
Since using Site Management in M2X, Ballance has reported significant improvements in its site operations. They've seen improved planning and customer satisfaction, and reduced errors and congestion at its sites, demonstrating M2X's effectiveness in managing congestion.
“The visibility is fantastic, it makes us so much more efficient, so simple to use, and there are no surprises anymore."
Service Centre Managers, Ballance
Lisa and Fiona
"M2X provides us the visibility of our freight task across our entire network in one place. It's easy to use, intuitive, clear - all the information is right there at your fingertips."
Product Flow and Transport Manager, Ballance
Kent Clark
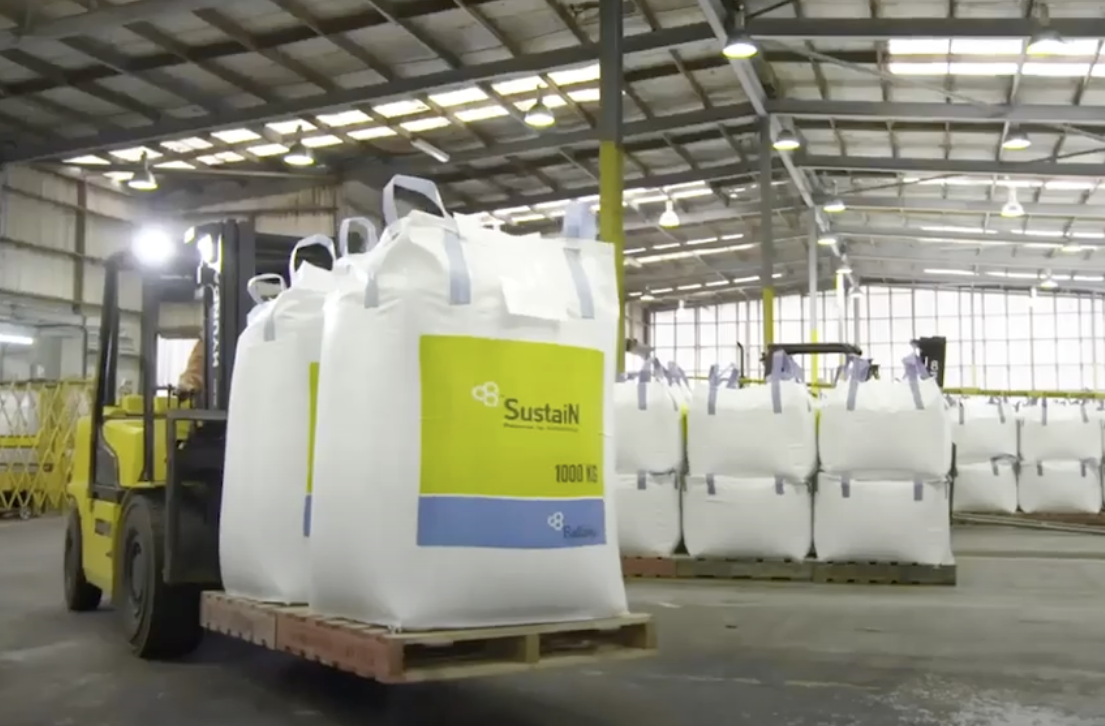
Conclusion
Site congestion is a significant challenge that impacts the efficiency and profitability of all stakeholders in the supply chain. However, with the implementation of an advanced TMS, these challenges can be effectively addressed. A TMS is an invaluable tool in managing site congestion, from improving communication and resource allocation to providing real-time tracking and automated processes. With its specialized features, M2X Site Management takes this a step further, offering a comprehensive solution to enhance efficiency, reduce detention costs, and improve customer satisfaction.